Automated Storage and Retrieval Systems: A Comprehensive Guide 2025
Are you looking to elevate your warehouse’s operational efficiency? Automated storage and retrieval systems are pivotal, enabling rapid and precise inventory handling through robotics and control software.
Table of Contents
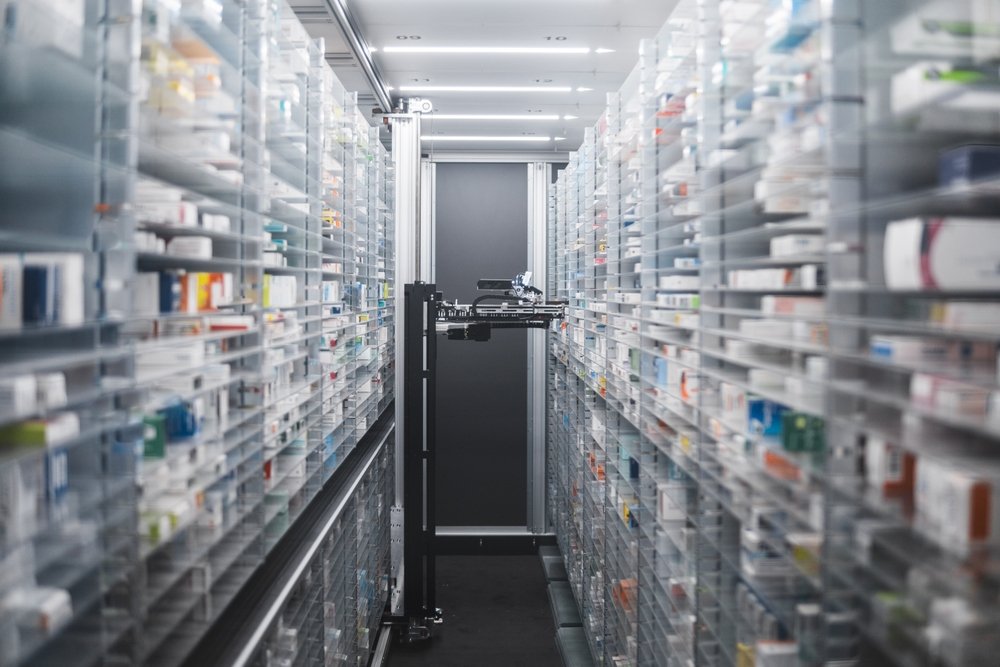
This guide delves into the fundamentals of AS/RS, breaks down their components, and highlights their critical role in modern logistics. It aims to enhance your decision-making for warehouse management.
Key Takeaways
- AS/RS systems are essential for automating high-volume storage and retrieval tasks in warehouses. They rely on key elements like SRMs, conveyors, and WMS to function efficiently and adapt to different storage environments, including refrigerated warehousing.
- AS/RS technology developments have evolved from early automated load handling to modern systems integrating digital automation software, high-bay warehouses, and robotics, leading to increased storage density, throughput, and reduced reliance on manual labor.
- Choosing the right AS/RS system depends on operational requirements such as product volume, order frequency, and space constraints. Businesses must assess potential system scalability, ongoing maintenance needs, and compatibility with existing warehouse management systems.
Understanding Automated Storage and Retrieval Systems (AS/RS)
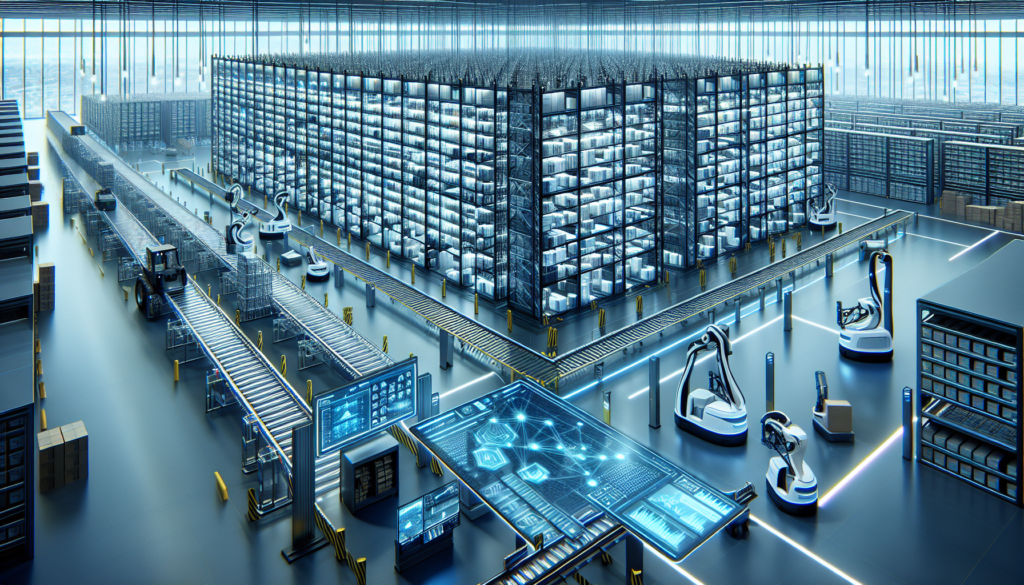
At its core, an Automated Storage and Retrieval System (AS/RS) is a technologically advanced system facilitated by robotics and computerization that optimizes the storing and fetching goods within a warehouse setting, embodying the integration of retrieval systems and automated storage. This system comprises several critical components, including:
The infrastructure of the automated storage system for holding inventory
- The machinery used for storage and retrieval tasks, including storage and retrieval machines (SRM)
- Interfaces for material transport
- Control software administered through a Warehouse Management System (WMS)
These systems are frequently deployed in operations that require fast-paced, accurate handling of substantial volumes with varying dimensions, velocity, and cost efficiencies. They provide numerous benefits to warehouse operations processes.
Pro Tips: A few notes about ASRS systems before you fall in love.
- They are very expensive, take almost a year to install/configure, and typically require building an extensive WMS interface,
- The cube utilization is around 50% or less, depending on the size of your products. This calculation was based on a vitamin and supplement model (very low cube items).
- You must put the same number of units into the ASRS as you take out. If entry/exit points are limited, this will be a constraint.
- The pick rates are very attractive, but when multiple stops are needed to complete the order, the conveyor can become the constraint.
Key Components of AS/RS
A typical AS/RS system is comprised of the following components:
- Defined storage locations within storage racks that organize items for efficient retrieval and stowage.
- Machines specifically designed for storing and retrieving goods transport these items to their respective spots on the racks.
The conveyors function as elements of the in/out systems, aiding in circulating products throughout the premises. Meanwhile, inventory management software integrated into a computer management framework monitors stock specifics and orchestrates all related activities related to storage and retrieval functions. This ensures that AS/RS processes run seamlessly.
How AS/RS Works
AS/RS systems employ various technologies to facilitate the automation of storage and retrieval tasks. For example, robotic horizontal carousel AS/RS configurations utilize an arrangement that includes three levels of carousels paired with an inserter/extractor mechanism, complemented by a takeaway conveyor system and an operative workstation.
In contrast, Shuttle-based AS/RS models deploy shuttles that navigate directly to the exact location where products are stored to secure the tote or carton containing the needed items.
These systems integrate AI-driven robots with sensors and cameras closely monitoring inventory quantities.
This capability allows immediate inventory status updates while improving operational efficiency via anticipatory restocking strategies.
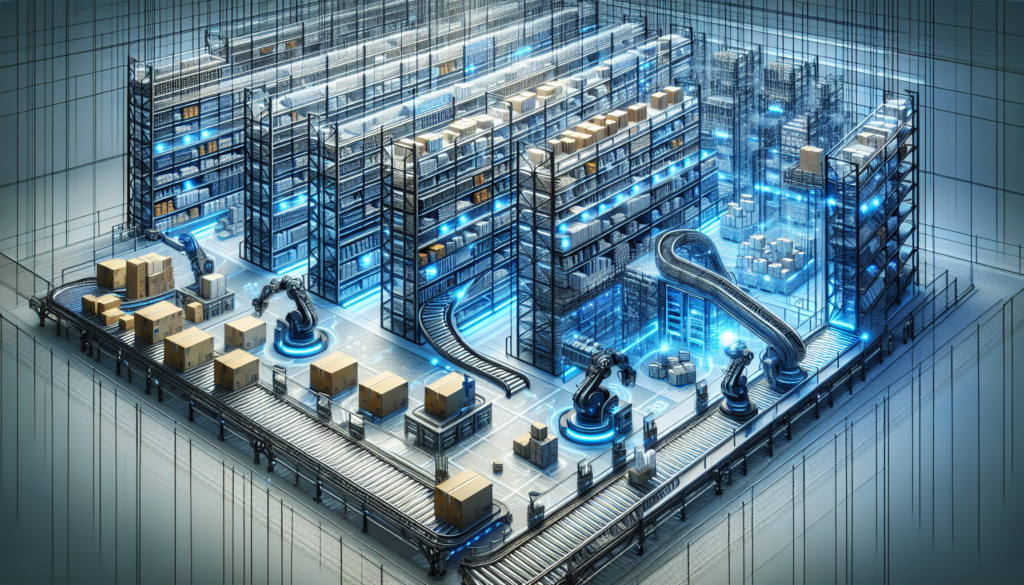
The Evolution of AS/RS Technology
From its genesis in the 1950s, AS/RS technology has witnessed considerable advancements. The pioneering installation of an AS/RS by Demag, a German firm, transformed warehousing technology with a novel integration of automation and the strategic utilization of vertical space.
Following this innovation, AS/RS systems have consistently grown globally. Recent developments have incorporated digital automation software into high-bay warehouses and minimized the need for manual labor within these automated storage systems.
Modern Advancements
Over time, AS/RS technologies have developed considerably. These systems now oversee intricate functions, with digital automation software orchestrating a variety of digital, robotic, and racking elements to suit different types of products and the scale of various warehouses.
High-bay warehouses are an example. Some soar as high as 150 feet, representing a marked decrease in reliance on human labor for warehouse operations.
There is a growing preference for adaptable and scalable AS/RS solutions that can be swiftly modified in response to fluctuating business needs and market pressures.
Different Types of AS/RS Systems
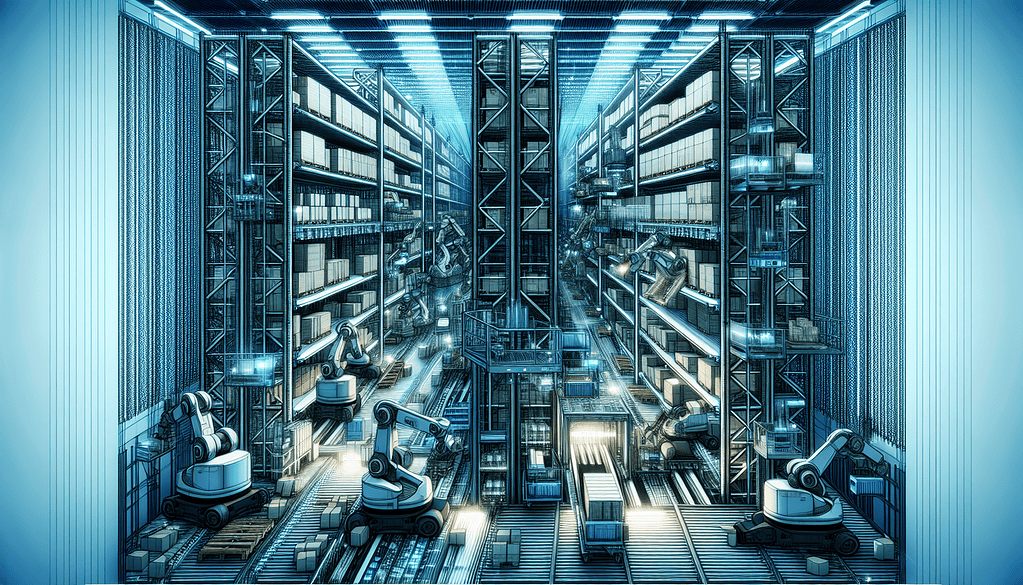
AS/RS systems are tailored to diverse storage and retrieval requirements, eschewing a universal solution. These systems fall mainly into unit-load and mini-load, each serving distinct needs.
Unique AS/RS types exist, such as the Go-Fer Bot AMR and Vertical Sequence Module (VSM), engineered to provide dense buffering and individual tote sequencing in bustling warehouse operations.
Another type of AS/RS system is the Vertical Lift Module (VLM), an enclosed dynamic storage solution optimizing space efficiency by automatically locating and retrieving trays of stored items with high-speed throughput rates.
Unit-Load Systems
AS/RS systems for unit loads are engineered to accommodate hefty pallets, providing solutions that optimize high-density storage. They can handle substantial load weights, from 1,000 to 5,500 pounds.
The unit-load AS/RS configurations feature towering storage racks reaching heights close to 40 feet and primarily come in two variations: fixed-aisle and moveable aisle cranes. These iterations enable effective organization and retrieval of pallets even within the confines of narrow aisles.
Mini-Load Systems
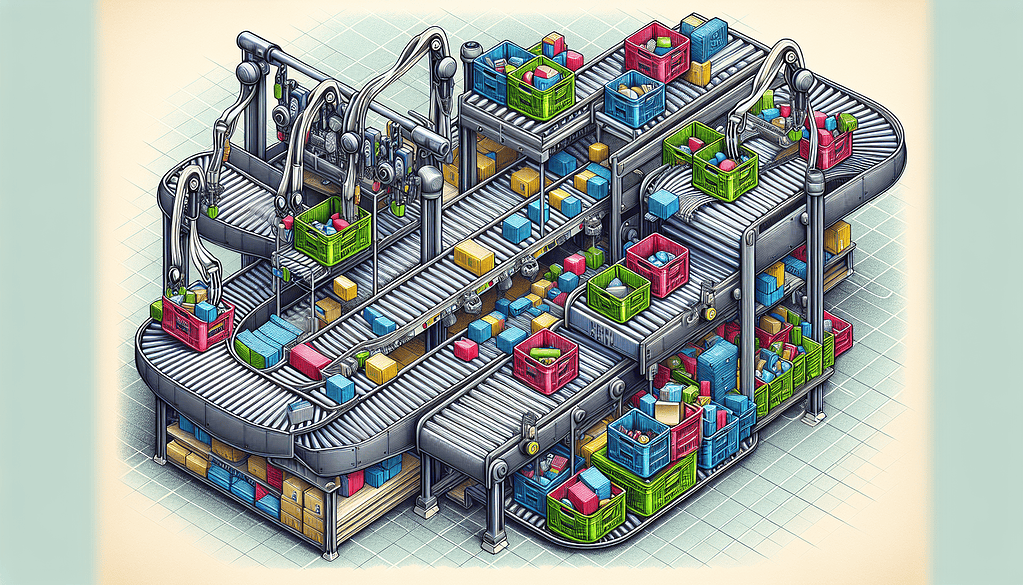
Mini-load Automated Storage and Retrieval Systems (AS/RS), commonly called ‘case-handling’ or ‘tote-stacking’ systems, are adept at managing smaller units like trays, cartons, and totes.
These systems can support items weighing up to 75 pounds and are highly beneficial for facilities with an extensive assortment of SKUs.
However, they are limited by the amount of floor space available for providing individual pick faces for each SKU. They act as flexible buffers while effectively replenishing storage designated for picking tasks.
Vertical Lift Modules (VLMs)
Vertical lift modules (VLMs) are a variant of Automated Storage and Retrieval Systems (AS/RS) engineered to optimize floor space efficiency within warehouse environments. These systems feature an enclosed framework that houses columns of trays with a central inserter/extractor mechanism.
Operating on the Goods-to-Person principle, VLMs deliver stored items straight to the operator, thus streamlining the picking process and enhancing its effectiveness.
Pros and Cons of Implementing AS/RS
Automated Storage and Retrieval Systems (AS/RS) offer a dual-edged sword in warehouse operations. They serve to automate tasks associated with inventory storage and retrieval, thereby streamlining processes.
They bring along the necessity for substantial infrastructural modifications and carry hefty initial expenses owing to their intricate nature. Additionally, AS/RS systems are designed to save floor space, optimizing warehouse layout by replacing large shelving areas with compact, efficient storage solutions that improve safety and increase overall productivity.
Benefits
AS/RS systems enhance warehouse operations by amplifying storage density, diminishing labor expenses, boosting safety protocols, and improving overall efficiency. Key advantages offered by sophisticated units such as the Go-Fer Bot AMR include:
- Elevated high-density storage
- Optimized throughput capacity
- Increased agility
- Substantial return on investment
These systems adeptly manage order staging within buffer storage areas pending suitable shipping intervals, thereby elevating precision and punctuality in dispatching goods and considering a return on investment typically achieved within the approximately a day five-year time frame, the compelling value proposition of AS/RS solutions.
Challenges
While advantageous, introducing AS/RS systems can come with specific obstacles. Shuttle-based variants of these systems may face issues such as restricted access to aisles when undergoing maintenance and a demand for larger space requirements compared to other options, which could impede the scalability of operations.
There are particular limitations tied to carousel-based AS/RS setups.
- Expansion complexities
- Significant floor space requirement
- Challenges in adapting to limited-space facilities
- Maintenance-related operational delays that affect productivity and disrupt the flow of work processes.
Choosing the Right AS/RS System for Your Business
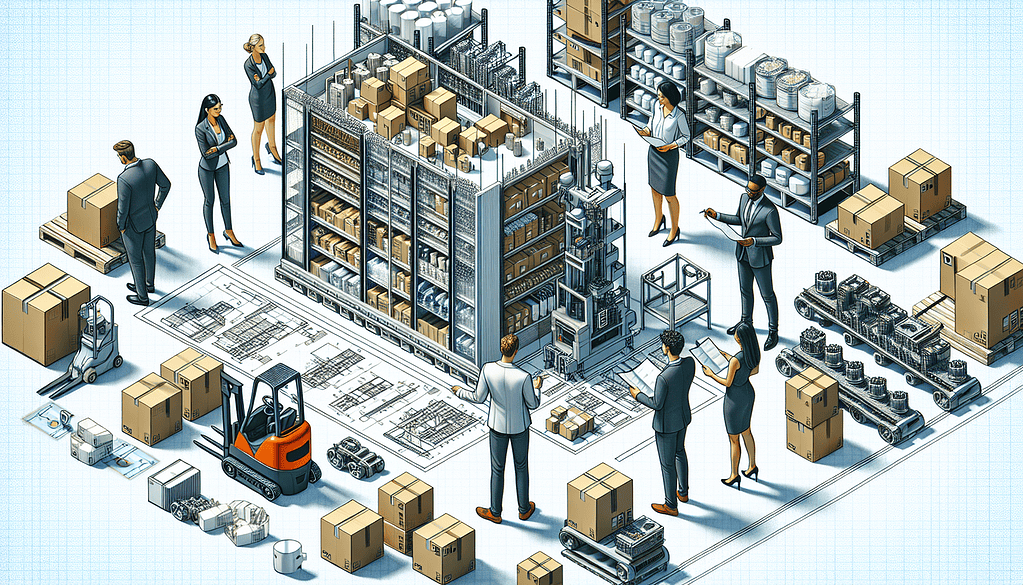
Selecting an appropriate Automated Storage/Retrieval System (AS/RS) for your company may seem daunting due to the many choices on offer. Yet, the secret to a successful choice hinges on matching the system you pick with the particular needs and hurdles your operations face.
Assessing Your Needs
Evaluating your operational requirements is essential to selecting the appropriate Automated Storage/Retrieval System (AS/RS).
This evaluation should include examining your business objectives, seasonal fluctuations in demand, expenses related to labor and hiring difficulties, limitations on warehouse space, necessities for managing inventory effectively, and issues relating to employee ergonomics.
When analyzing these factors, you must consider the volume and nature of goods handled, the frequency of orders processed, the variability of Stock Keeping Units (SKU), and the dimensions of available storage areas.
When assessing AS/RS systems for potential implementation within their operations, companies should focus on how these systems can enhance asset utilization while optimizing spatial use within warehouses and workforce productivity.
The goal is to identify an AS/RS that delivers maximum value through improved management of physical resources, such as space efficiency, along with reduced labor costs.
Comparing Systems
After grasping what your requirements are, you should proceed to assess various Automated Storage/Retrieval Systems (AS/RS) by considering the following factors:
- Cost of systems
- System storage and retrieval capacities
- Potential for expansion
- Regular maintenance requirements
- Integration with current warehouse management software
When choosing a provider, it’s important to consider their proficiency in setting up the system, its dependability, and the level of customer service offered after making a purchase.
Implementing and Maintaining an AS/RS System
Implementing and upkeeping an AS/RS requires a well-planned strategy. Important points to consider include:
- Adopting a staggered implementation and exploring various financing methods can help make the transition smoother and more financially viable.
- Guaranteeing that the new system works seamlessly with current warehouse operations is crucial.
- It’s imperative to devise a forward-thinking maintenance plan to ensure continuous, efficient system operation.
Integration with Existing Operations
Incorporating an AS/RS into present workflows is a pivotal aspect of the setup process. It’s essential that these advanced automated systems align with the preexisting Warehouse Control System (WCS) or Warehouse Management System (WMS) to preserve operational effectiveness and optimize throughput.
Choosing an appropriate AS/RS system for integration also requires assessing its software dependability, physical attributes, and capabilities.
Ongoing Maintenance and Support
Implementing an AS/RS necessitates a commitment to regular maintenance and support to ensure its long-term efficiency. Key steps include:
- Cultivating robust relationships with vendors for continuous support and rapid resolution of problems
- Securing service contracts that guarantee swift maintenance services
- Providing thorough training for employees and internal staff to enable them to operate the system effectively and undertake preventative maintenance tasks
Future Trends in AS/RS Technology
Thanks to the ongoing introduction of innovations, the future shines brightly for Automated Storage and Retrieval System (AS/RS) technology.
A surge in its adoption is seen as advancements present various choices regarding size, speed, affordability, and adaptability.
Since the 2000s, groundbreaking robotic models boasting both upper and lower extremities have entered the market.
These are outfitted with technologies such as radar, computer vision, or sensors that enable them to recognize goods and handle loading and unloading tasks.
Robotic systems powered by artificial intelligence significantly enhance warehouse operational efficiency by learning from their surroundings, forecasting maintenance demands, and bolstering safety measures.
Robotics and Artificial Intelligence
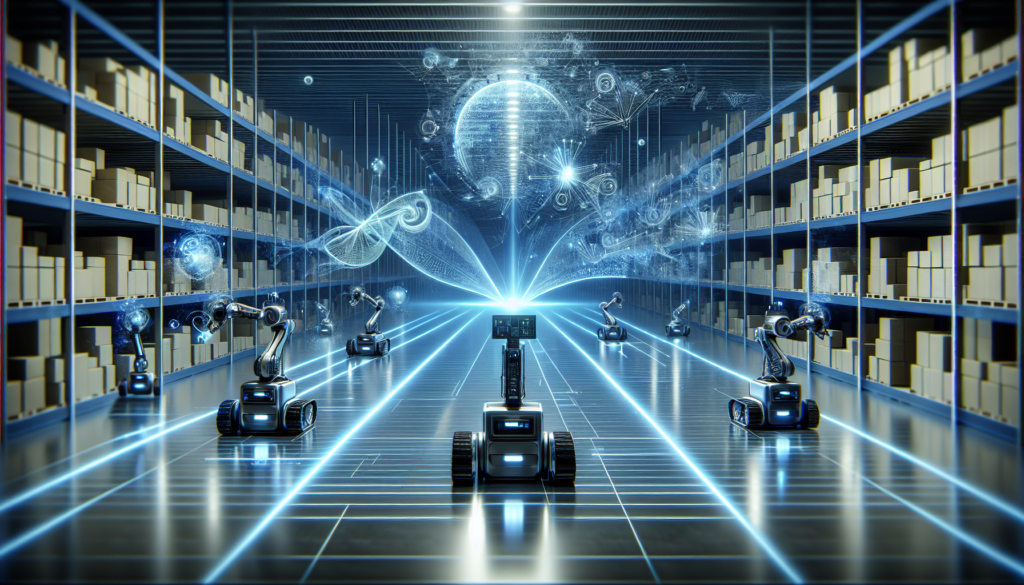
The integration of artificial intelligence and robotic technology into Automated Storage/Retrieval Systems (AS/RS) has increased.
Autonomous Mobile Robots (AMRs), such as the Stacker-Bot AMR and the Go-Fer Bot AMR, improve AS/RS functionalities by offering adaptable, high-density storage solutions at lower costs, coupled with sophisticated sensor suites that enhance their flexibility, efficiency, and capacity to scale.
Progress in sensor innovations and machine learning algorithms has greatly enhanced the overall automation efficacy of mobile robots. These improvements have also bolstered these systems’ safety and predictive maintenance features.
Internet of Things (IoT) and Smart Warehousing
Another emerging trend is enhancing the efficiency and productivity of Automated Storage/Retrieval Systems by integrating the Internet of Things (IoT).
With IoT, businesses gain better access to data and real-time tracking capabilities, which allows them to refine their inventory management processes, streamline their workflows, and make decisions based on accurate information.
Summary
Introducing AS/RS systems transforms warehouse operations through automated precision and their capacity for high-density storage. To capitalize on these systems’ full capabilities, systems must select an appropriate system that aligns with their requirements, guarantees a smooth integration within current operational frameworks, and provides consistent support and maintenance.
Ongoing developments in AI, robotics, and IoT advanced technologies are expected to yield efficiency and enhancements within the warehousing sector in future scenarios.
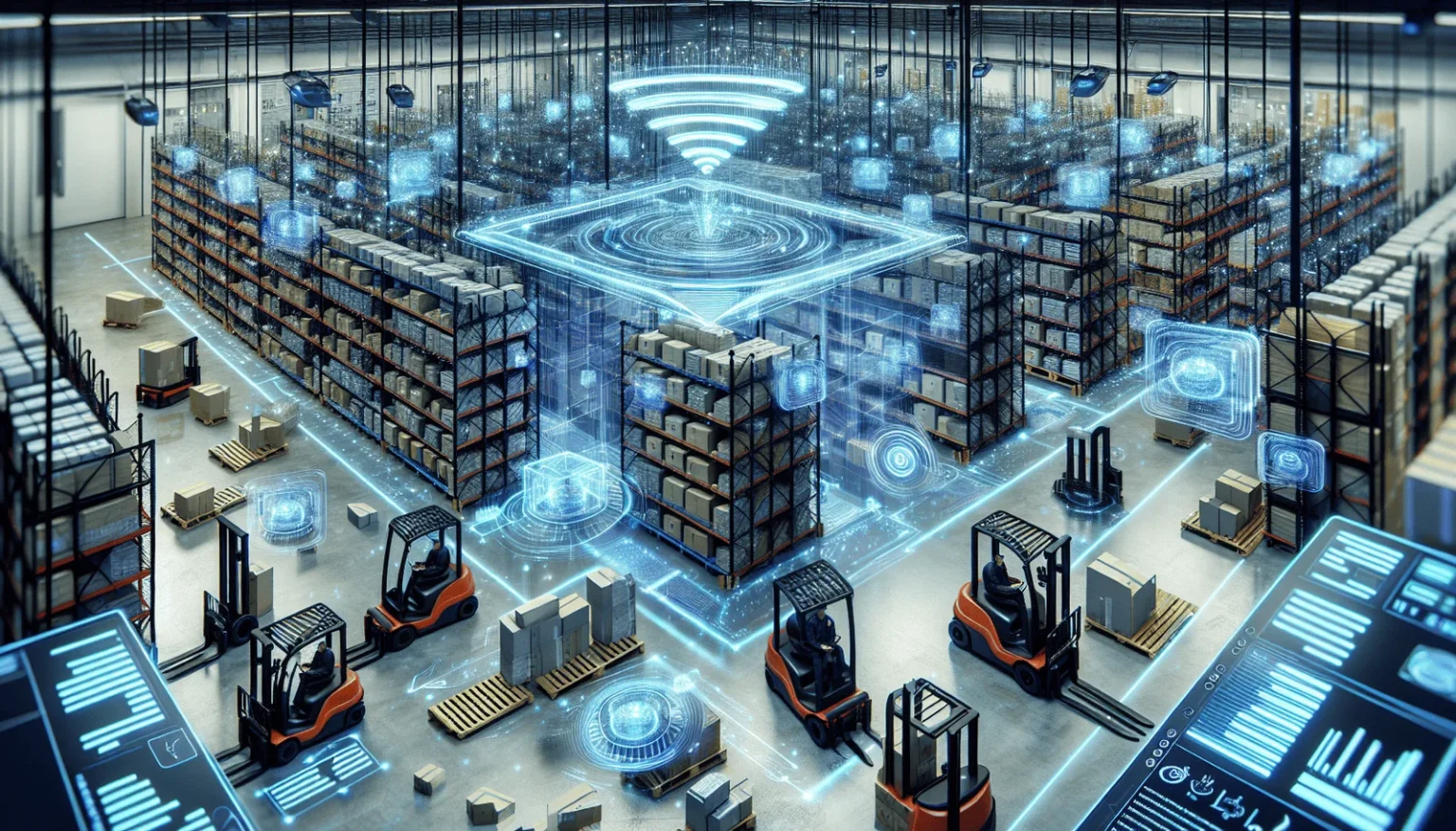
FAQs (Frequently Asked Questions)
What is an AS/RS?
A computer and robot-assisted AS/RS enhances storage and retrieval processes in warehouse settings. This system encompasses crucial components like the structure for storing goods, a machine dedicated to both storage and retrieval tasks, conveyance interfaces, and software designed for control purposes.
How does an AS/RS system work?
A system known as AS/RS enhances efficiency by automating storage and retrieval procedures. It utilizes different technologies, including robotic carousel systems, shuttle-based mechanisms, and AI-powered robots.
It contributes to enhanced operational effectiveness via predictive restocking methods and precise monitoring of inventory levels.
What are the benefits of implementing an AS/RS system?
Incorporating an AS/RS) can enhance warehouse efficiency by increasing storage density, cutting labor expenses, boosting safety protocols, and improving both the precision and scheduling of shipments. This approach serves as an all-encompassing strategy for refining warehouse operations.
What are some challenges of implementing an AS/RS system?
Implementing an AS/RS system can be challenging due to the need for significant infrastructure changes, high upfront costs, and limitations with certain types of systems. These challenges include maintenance access issues and demanding substantial floor space.
What are some future trends in AS/RS technology?
Advancements in robotics, artificial intelligence, and Internet of Things connectivity are expected to be at the forefront of future trends within automated storage and retrieval systems (AS/RS) technology. These enhancements aim to elevate the efficiency and effectiveness of these systems significantly. Progress is poised to transform automated storage & retrieval system capabilities by enabling better data access and real-time tracking through ongoing developments.