Enhance Your Floor Plan for Warehouse Operations Now – 2025
Is your warehouse a chaotic jumble of pallets, picking a daily obstacle course? Are your associates experts at playing Tetris? Do you need a better floor plan for warehouse operations?
Table of Contents
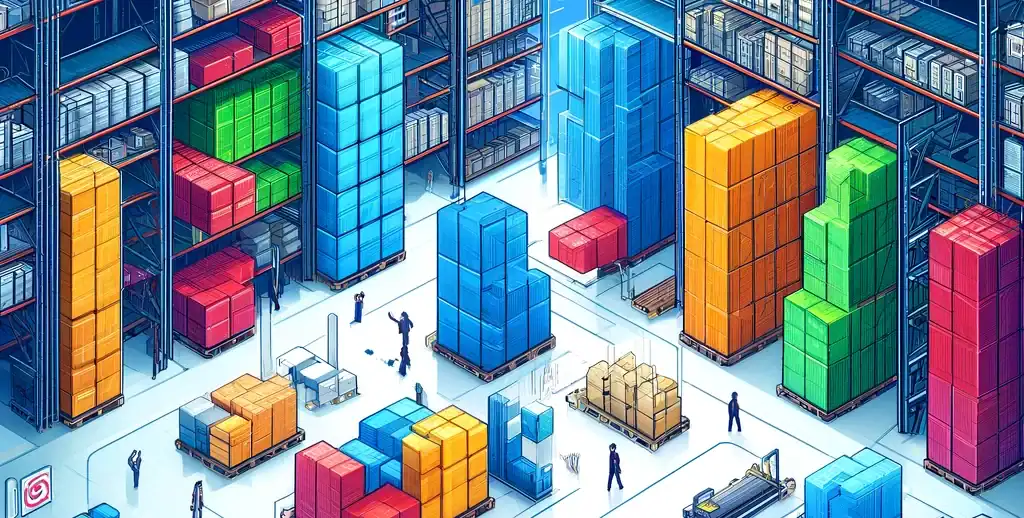
This guide is your ultimate playbook, packed with actionable steps to transform your warehouse into a productivity powerhouse. We’ll ditch the complexity and show you how to leverage design tools, optimize traffic flow, and make smart choices that maximize space, ensure safety, and keep your budget on track.
Key Takeaways
- An efficient warehouse layout must carefully balance storage needs against space required, considering inventory characteristics and using software for optimal layout and traffic flow visualization.
- Maximizing storage utilization involves innovative solutions like intelligent systems, optimizing aisle widths, and making full use of vertical space adaptable for future growth.
- Selecting the correct storage and material handling equipment is essential for efficiency. Designing for safety, compliance, and streamlined order fulfillment processes is also essential, and warehouse software plays a key role.
Crafting Your Warehouse Floor Plan
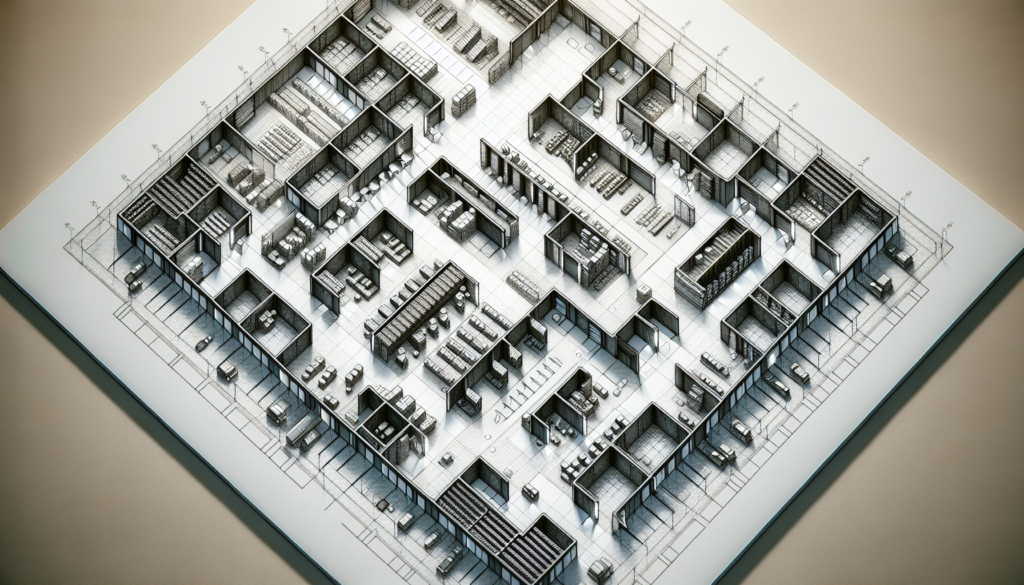
Creating an efficient warehouse layout requires the following:
- A well-planned strategy
- Utilization of the latest technology
- Accounting for staff training, their needs, and sustainable practices
- Adhering to financial limitations
Undertaking this challenge can be demanding. The benefits it brings are substantial.
Assessing Your Space Needs
Commencing this procedure requires an assessment of your spatial requirements. The characteristics of the items you wish to store will greatly influence the amount of square footage necessary for your storage areas.
Your warehouse plans should include factors such as inventory dimensions, form, volume, and any unique storage needs they may possess.
Achieving operation efficiency hinges on striking an optimal equilibrium between space dedicated to storage and usable floor area.
Plotting the Layout
When you’ve determined the necessary space, it’s time to draft your warehouse layout. Software is extremely useful for this stage, as it lets you create and experiment with different layouts virtually.
This eliminates the need for constant rearrangements. Examining a range of warehouse layout examples through such software allows you to discover the optimal design that meets your requirements.
Visualizing Traffic Flow
Ensuring an uninterrupted flow of operations is essential, and it can be achieved by carefully designing your layout to facilitate visualizing your traffic flow. This step is paramount for reducing interruptions and enhancing operational efficiency. It also allows you to simulate forklift traffic.
Maximizing Warehouse Space Utilization
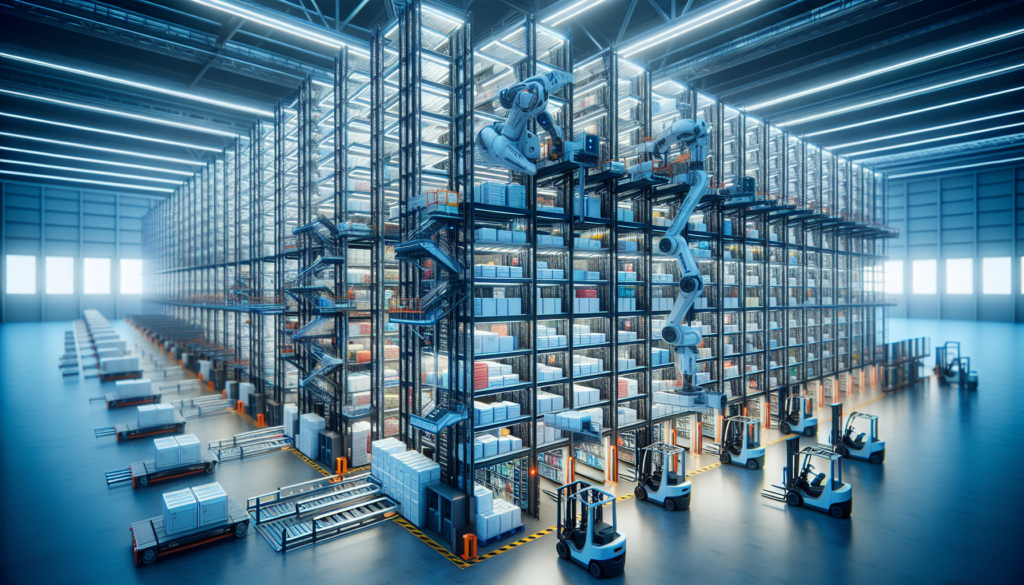
When you have mapped out your layout and anticipated traffic movement, your subsequent priority should be to optimize space use.
This requires exploring creative methods for exploiting the space by integrating smart storage equipment, fine-tuning aisle widths for efficiency, and utilizing currently underutilized spaces.
Did you know that most warehouses only utilize around 20% of their storage space? That wasted space translates into wasted money, impacting everything from utilities to worker throughput.
Your storage utilization is critical in today’s competitive logistics landscape.
Intelligent Storage System Placement
By introducing smart storage equipment, you can substantially enhance the utilization of your warehouse space. This includes employing vertical and horizontal carousels or movable shelving units to maximize areas where floor space is at a premium.
Applying AI-driven optimization methods can refine and improve the efficiency of the entire warehouse floor plan.
Optimizing Aisle Widths
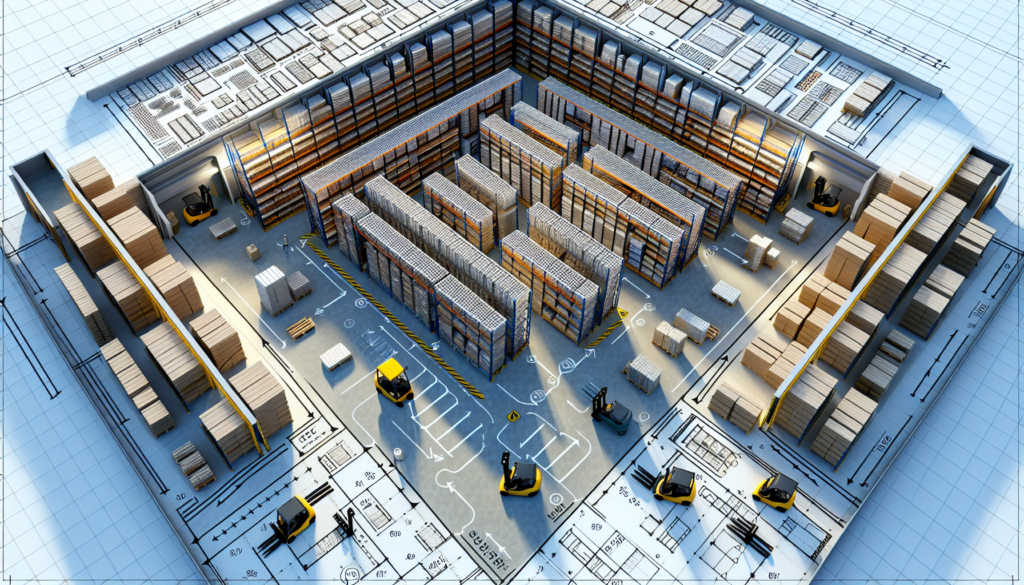
One can enhance storage utilization by strategically placing storage space and fine-tuning the aisle layout to be large enough for essential equipment yet compact. This process balances the need for accessibility with conserving valuable floor space.
Here are our recommendations for aisle widths:
- Wide Aisles (WA): Typically ranging from 10 to 12 feet wide. These are ideal for standard sit-down counterbalanced forklifts and frequently accessed pallet inventory. They offer ample space for maneuvering and are common in traditional warehouses and distribution centers.
- Narrow Aisles (NA): These are narrower, typically 8 to 10 feet wide. They are suited for narrow aisle forklifts, which are more compact. This allows for increased storage density at the cost of some maneuverability.
- Very Narrow Aisles (VNA): As the name suggests, these are the tightest spaces, typically less than or equal to 6 feet wide. They require specialized, narrow aisle trucks such as turrets and swing-reach forklifts operating on wire guidance. Order pickers (stock pickers) are also good candidates for very narrow aisle travel.
Wire Guidance in Aisles
Wire guidance is an electromagnetic system that automates steering for Very Narrow Aisle (VNA) forklifts navigating warehouse aisles. Here’s a breakdown of how it works:
- Installation: A guidewire is embedded in a shallow groove (½” – ⅝” deep) milled down the center of the aisle floor and sealed with epoxy, creating a closed-loop circuit.
- Operation: A Line Driver Unit (LDU) sends a low-voltage electrical current through the wire, generating an electromagnetic field. Sensors on the forklift detect this field and automatically steer the forklift to follow the wire.
Benefits of Wire Guidance
- Increased Productivity: With hands-free steering, operators can travel faster and pick products more efficiently.
- Space Optimization: Warehouses can have narrower aisles, maximizing storage capacity.
- Reduced Costs: Automatic guidance minimizes forklift damage to racks, products, and itself, leading to lower repair and replacement expenses.
- Enhanced Safety: Automatic slowdowns and stops for signal loss prevent collisions and operator injuries on the warehouse floor.
Here are some additional things to consider about wire guidance:
- It’s primarily used in warehouses with very narrow aisles and high-density storage.
- The system requires planning and professional installation for optimal performance.
- While the wire is buried, the LDU and other system components need space for placement.
Leveraging Vertical Space
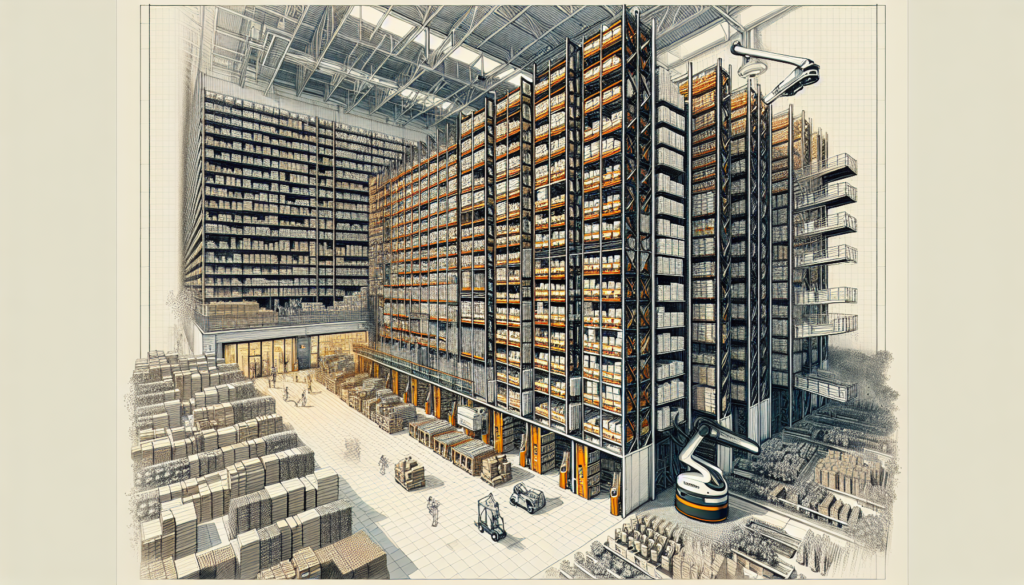
Finally, it is essential not to neglect the utilization of your vertical space. Solutions that use height, including pallet racks and mezzanines, can increase your storage capacity two or threefold without requiring the enlargement of your warehouse’s physical space.
Selecting the Right Warehouse Equipment
Optimizing your warehouse for efficient operations is as important as choosing the appropriate equipment. This requires assessing the kind of items being stored, evaluating the available space, and ensuring that your overall efficiency is taken into account in your warehouse floor plan.
Equipment for Storage and Retrieval
You have various storage systems and retrieval equipment options, each designed to optimize efficiency within your operations. Choosing appropriate equipment is key to boosting your capabilities, whether cantilever racks tailored for bulky items or bins for assembling and storing smaller parts.
Material Handling Essentials
Effective material handling is crucial in operations. Proper equipment, such as forklifts, pallet jacks, and conveyor systems, can enhance operational flow, bolster efficiency, and diminish the likelihood of accidents or injuries in the warehouse setting.
Designing Warehouse Layout for Adaptability
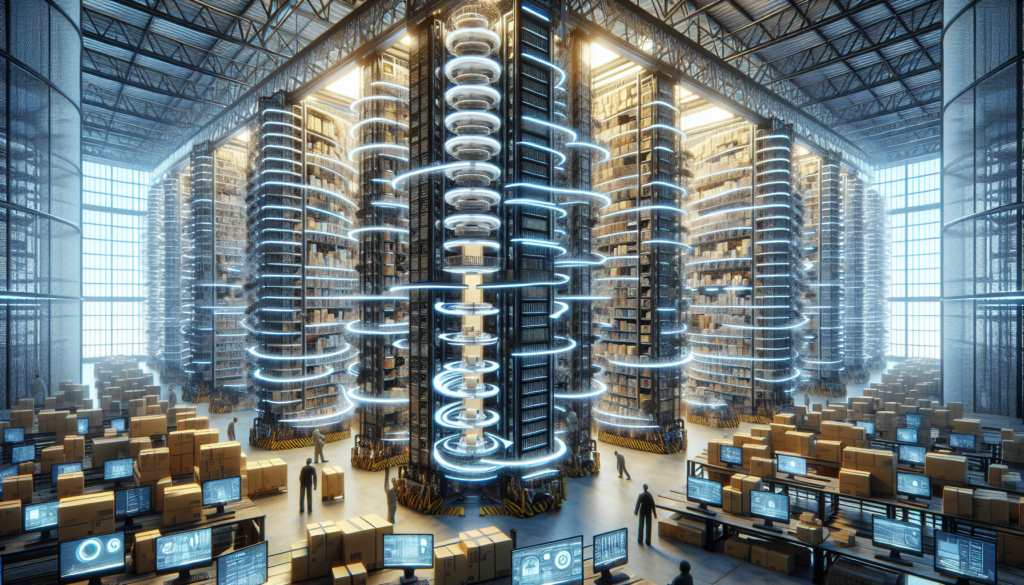
As your business grows and evolves, your warehouse must keep pace with this development. Planning for potential changes and aligning the design of your warehouse with long-term business goals are key steps to take.
Implementing flexible automation solutions will ensure adaptability within the space, readying it for future expansion needs.
Scalable Storage Solutions
Scalable solutions are crucial in your warehouse operation for adaptability and expansion. They allow systems such as the AutoStore to seamlessly adjust upwards or downwards in line with fluctuating inventory levels, maintaining consistent efficiency and enough space.
Flexible Work Areas
Equally crucial is the ability to rearrange and adapt workstations and packing zones to meet varying operational demands. Modular furniture can be easily reconfigured or expanded to manage periods of high volume or unique tasks.
Streamlining Order Fulfillment Processes
Optimizing operations includes enhancing order fulfillment by arranging items in high demand near the shipping areas. This streamlines tasks that require significant labor and implements lean management principles for more efficient processes.
Efficient Picking Strategies
Efficient warehouse design and advanced software can streamline picking strategies, vital for expediting order fulfillment. Effectively organizing inventory, employing strategic picking paths, and incorporating conveyor systems technology can significantly enhance efficiency.
Staging and Packing Area Design
It is essential to consider the layout of staging and packing zones carefully. These spaces need to be organized to maximize efficiency while factoring in the supplies and the approaches for restocking them.
Incorporating Safety and Compliance
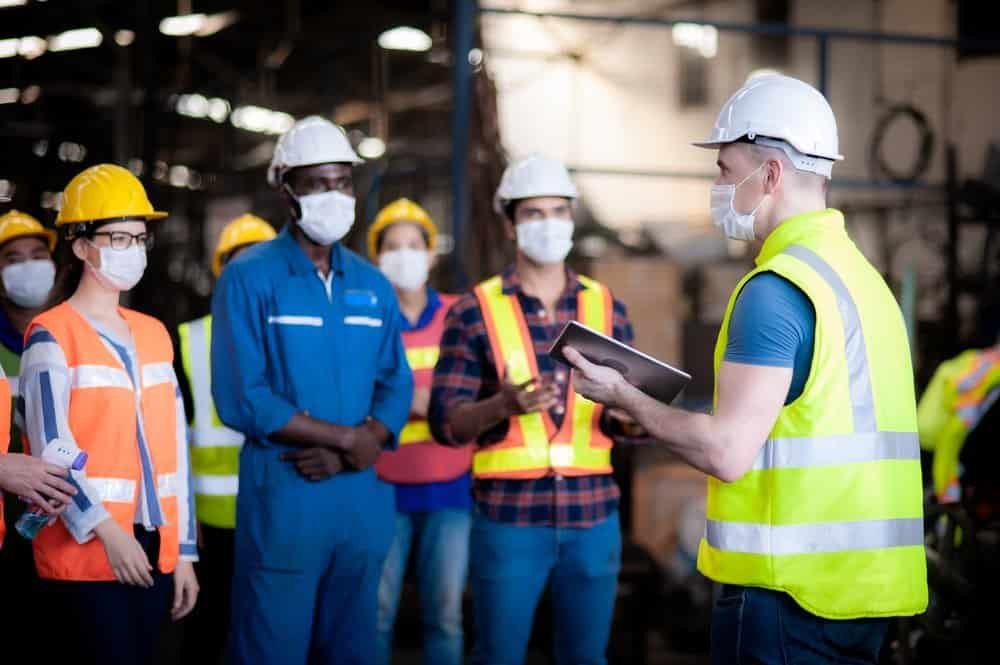
Regardless of efforts to optimize operations, safety and compliance remain paramount. Fundamental safety protocols must be in place, and a simple and restrained color palette for floor markings must be utilized so employees can swiftly recognize various zones within the warehouse and any potential risks associated with them.
Safe Navigation and Emergency Exits
Ensuring safety within a warehouse depends on several key factors.
- Facilitating secure movement throughout the facility
- Having emergency exits that are visibly labeled
- Compliance with local authority regulations and OSHA requirements concerning the floor plan design
- Ensure routes designated for emergency evacuations are free from dangerous substances and avoid leading into confined spaces.
Ergonomic Considerations
In designing your warehouse, it’s crucial to integrate ergonomic principles into the layout of workstations and various zones within the facility. This approach ensures that accessibility and safety are enhanced throughout your warehouse design, focusing on ergonomics considerations.
Utilizing Floor Plan Design Software
Employing software to develop a floor plan can greatly streamline the creation of a warehouse layout. Planning for such a layout involves maximizing storage utilization, improving workflow efficiency, and guaranteeing the safe use of material-handling equipment within the warehouse.
Benefits of Using Software
Design software offers a multitude of advantages for warehouse layout operations, such as:
- Lowering operating expenses through your supply chain
- Enhancing productivity levels
- Boosting safety measures
- Aiding in the precise creation of warehouse layouts
- Enabling the visualization and experimentation with different setups before the actual execution
Examples of Warehouse Planning Tools
Numerous tools for creating floor plans exist, such as SmartDraw and EdrawMax Online, which supply users with examples of floor plans. They feature easy-to-use interfaces, diverse templates, and sophisticated functionalities like separate layers to manage electrical, plumbing, and HVAC systems.
They are equipped with libraries full of floor plan concepts and warehouse planning charts to inspire and spark warehouse layout design.
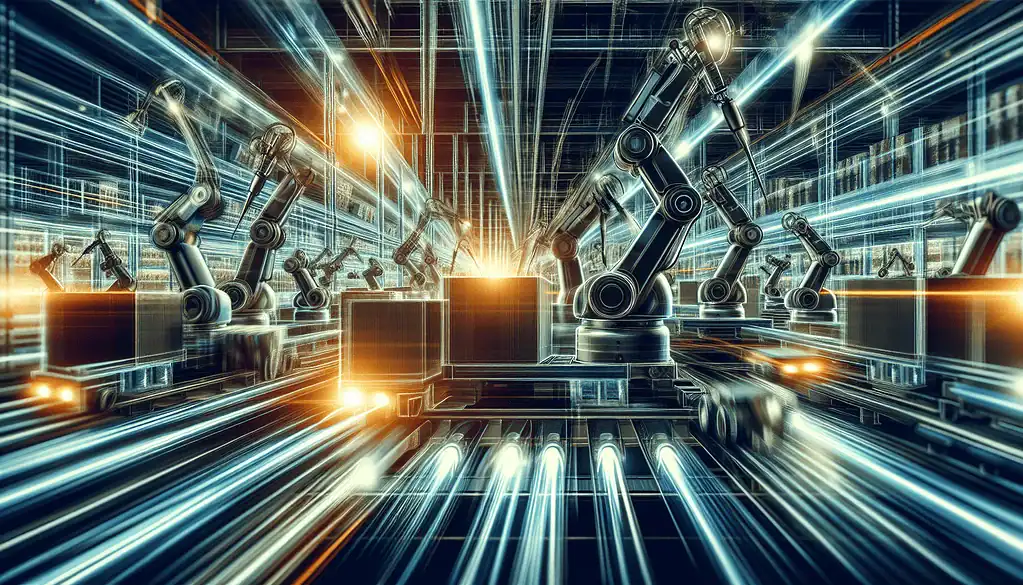
Summary – Floor Plan for Warehouse
Enhancing a warehouse floor plan requires meticulous design and planning and appropriate equipment. Evaluating your space requirements, drafting an effective layout, optimizing space use within the warehouse, and choosing suitable equipment are all critical steps contributing to a highly efficient and productive workflow.
Frequently Asked Questions
Q: What is the best layout for a small warehouse?
The optimal layout for a small warehouse floor is the U-shaped configuration, which positions inbound and outbound loading docks on parallel sides. Storage and picking zones are located centrally, ensuring seamless operational flow. You may also want to consider using third party logistics.
Q: How do I make a warehouse floor plan?
To craft an effective warehouse floor plan, adhere to these seven crucial steps: pinpoint the specific purpose of your space, construct a schematic representation, assess stock necessities, determine the necessary equipment, strategically allocate and enhance the use of space, simulate vehicular movement patterns within your setup to ensure efficiency and finally put into action the devised layout.
Q: What is a warehouse floor plan?
A warehouse plan is a carefully devised blueprint that details the arrangement and setup of various elements within the facility, such as inventory sections, pathways for picking items, areas designated for shipping, and stations for work tasks.
Q: How can warehouse space be maximized?
Utilize smart systems and optimize the aisle widths within your warehouse to enhance storage utilization and effectively use vertical space. This strategy will not only expand your capabilities but also elevate the productivity levels of your operations. This warehouse layout design planning is crucial for warehouse layouts.