Collaborative Robots in Warehousing: Benefits and Best Practices
Warehouse operations are under constant pressure to be faster, safer, and more efficient. Collaborative robots (cobots) are changing the game by working alongside human employees — not replacing them. Unlike traditional robots confined to cages, cobots are designed for safe interaction, adaptability, and seamless integration into warehouse workflows.
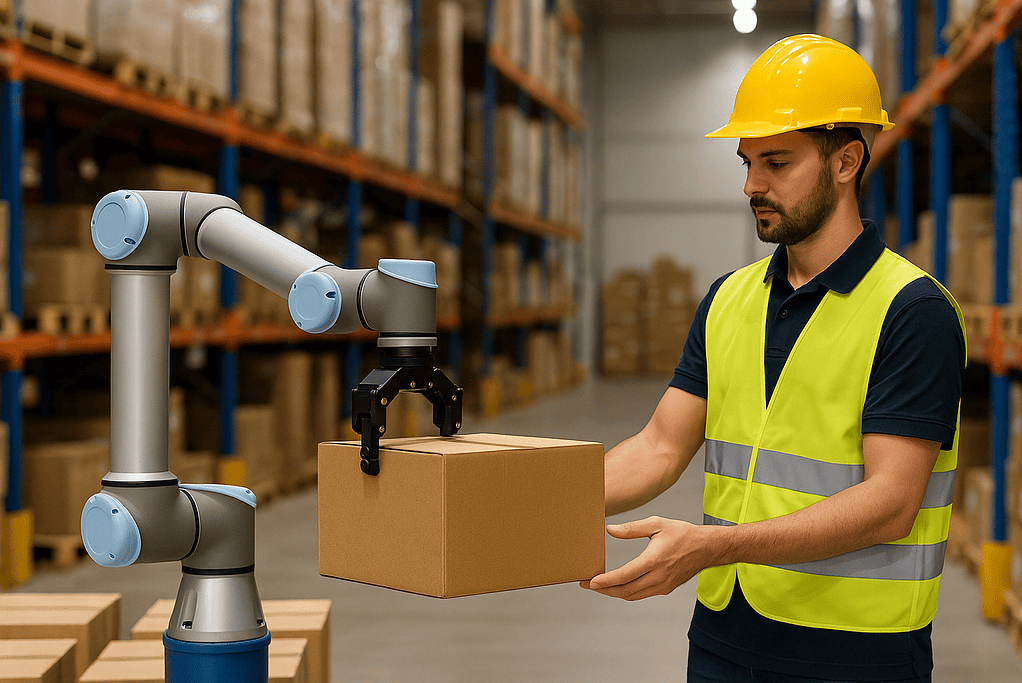
Key Takeaways
Collaborative robots (cobots) are designed to work safely alongside people in warehouse environments.
Benefits include improved safety, reduced repetitive strain injuries, and increased flexibility in handling tasks.
Cobots support tasks such as picking, packing, palletizing, and quality checks without requiring large infrastructure changes.
Successful adoption requires training, clear KPIs, and integration with WMS/WES systems.
What Are Collaborative Robots?
Collaborative robots, also known as cobots, are lightweight, flexible machines equipped with sensors and AI that enable them to safely operate in close proximity to humans. Unlike traditional industrial robots, cobots don’t require cages or fixed tracks. Instead, they can move, adapt, and collaborate with workers in real time.
Cobots are increasingly used in warehousing to handle repetitive tasks, such as picking, carton loading, and even machine tending, thereby freeing human workers to focus on higher-value activities.
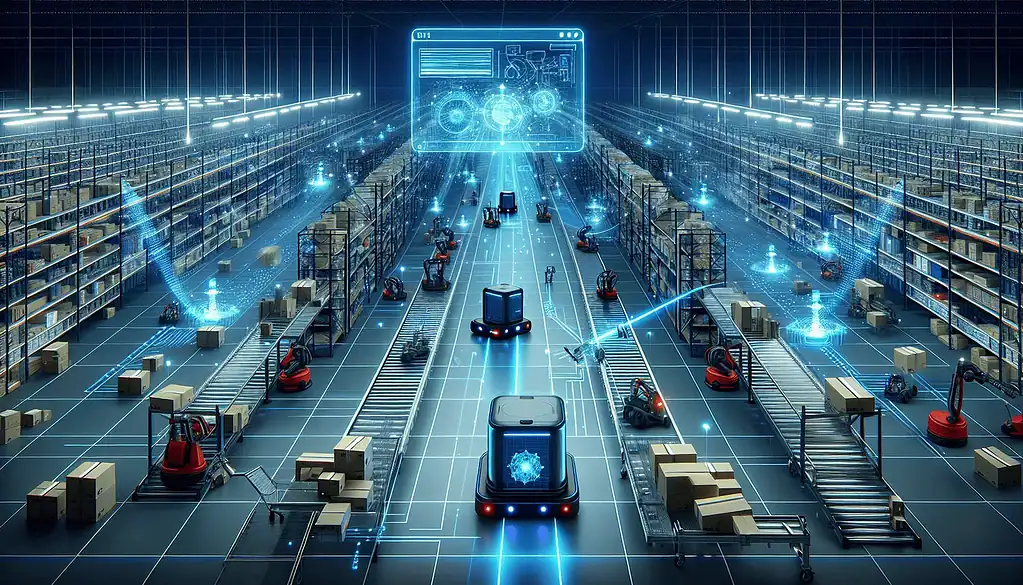
Benefits of Collaborative Robots in Warehousing
Improved Safety
Cobots are equipped with sensors and force limitations that prevent movement when encountering obstacles, thereby reducing the risk of accidents and injuries.
Enhanced Productivity
By automating repetitive or ergonomically risky tasks, cobots reduce fatigue and allow workers to focus on quality control and problem-solving.
Flexibility
Cobots can be redeployed quickly to new tasks. They integrate seamlessly with conveyor systems, pick stations, and even mobile robots, requiring minimal infrastructure changes.
Cost-Effective Automation
Compared to large-scale automation, cobots require lower upfront investment and can scale gradually as operations grow.
Common Warehouse Applications
Picking assistance: Cobots bring items to pickers or assist with sorting SKUs.
Packing and palletizing: They handle heavy lifting and repetitive stacking.
Sorting and quality control: Vision-equipped cobots detect defects or mislabels.
Material handling: Cobots support conveyors or AMRs by loading/unloading items.
These applications reduce bottlenecks and help meet tighter shipping deadlines.
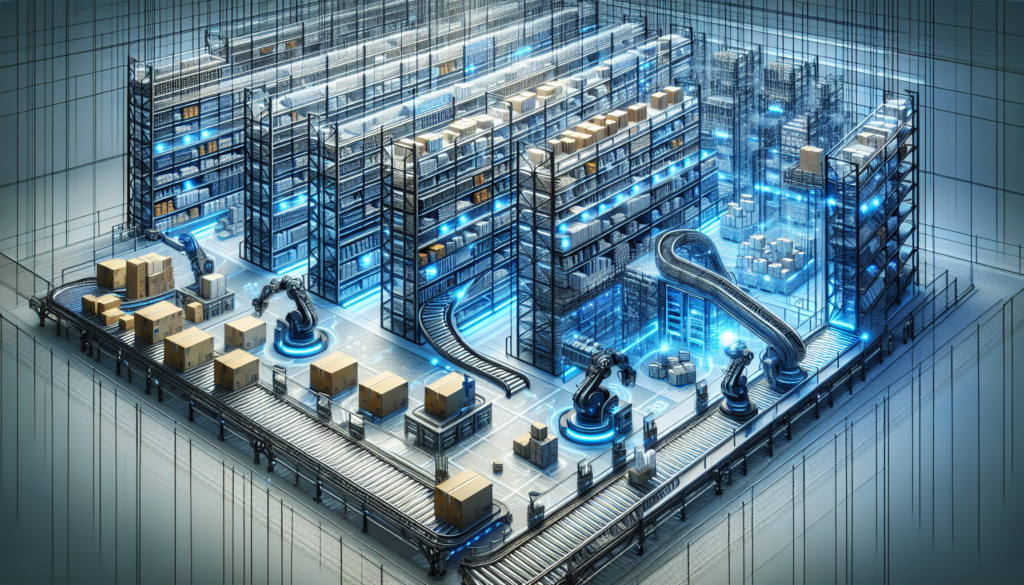
Best Practices for Implementing Cobots
Start Small: Begin with one task, such as palletizing, and scale as ROI is proven.
Train Employees: Workers must understand how to work safely and effectively with cobots.
Integrate with Systems: Cobots should connect with your WMS or WES for real-time task assignment.
Set KPIs: Track order accuracy, throughput, downtime, and labor savings to measure success.
Plan for Change Management: Address employee concerns early to encourage adoption.
Challenges to Consider
Upfront cost: Though lower than full automation, cobots still require capital investment.
Training curve: Teams need time to adapt to human-robot collaboration.
Integration complexity: Cobots may require middleware or custom interfaces to connect with legacy systems.
Addressing these challenges upfront ensures smoother deployment.
The Future of Collaborative Robots in Warehousing
As AI, vision systems, and machine learning continue to advance, cobots will become increasingly autonomous and capable of handling more complex tasks. Expect to see cobots working in hybrid teams with AMRs, drones, and humans, creating adaptive warehouses that strike a balance between flexibility and efficiency.
External Links
FAQs
What makes collaborative robots different from traditional robots?
Cobots are designed to safely work alongside people without cages or safety barriers. They’re flexible, adaptable, and suited for shared spaces.
How much do cobots cost?
Depending on the application, cobots range from $20,000 to $60,000 per unit, plus integration costs. ROI is often achieved within 1–3 years.
Can cobots replace human workers?
Cobots are not meant to replace workers but to assist them by taking on repetitive, labor-intensive, or unsafe tasks.
What warehouse tasks are best suited for collaborative robots (cobots)?
Picking, packing, palletizing, and quality control are the most common and effective applications.