System Directed Putaway: 7 Powerful Tips for Profiling Inventory
In the world of warehouse management, the difference between profit and loss often lies in the details – and sometimes, those details are as simple as where you put things. Trying to manually direct inventory off the dock based on predetermined is not sustainable. You need system directed putaway.
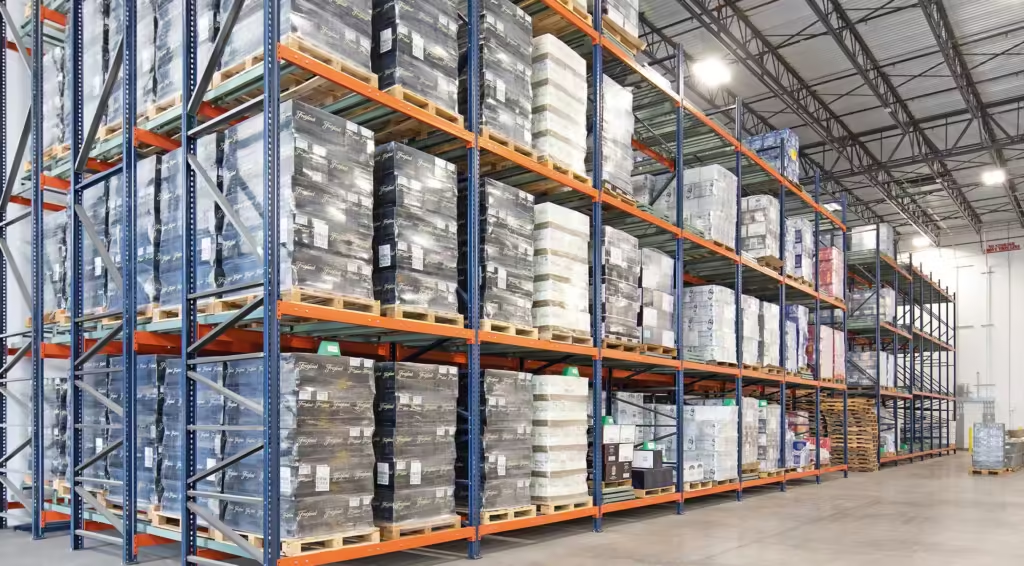
Introduction
In the fast-paced realm of modern logistics, warehouses serve as the beating heart of supply chains worldwide. Yet, amidst the constant flow of goods, one critical aspect often goes overlooked: the putaway process.
This seemingly mundane task of storing items upon arrival can be the key to unlocking significant efficiencies and cost savings.
Warehouses are complex ecosystems that manage receiving, storage, picking, packing, and shipping. Each process must work in harmony to ensure smooth operations.
However, the putaway process—the bridge between receiving and storage—is pivotal in determining the efficiency of all subsequent activities.
Efficient storage and retrieval are the cornerstones of warehouse productivity. When stored logically and accessibly, it dramatically reduces the time and effort required for picking and replenishment.
This efficiency ripples through the entire operation, affecting everything from labor costs to order fulfillment times and customer satisfaction.
Enter the game-changer: system-driven putaway. This approach moves beyond traditional, often arbitrary storage methods, leveraging data and technology to optimize item placement.
By considering item characteristics, picking methods, and order patterns, a system-driven putaway creates a strategic storage plan that aligns perfectly with your operational needs.
The following sections will explore system-driven putaway strategies, benefits, and real-world applications. You’ll discover how this approach can transform your warehouse operations, significantly reduce costs, and position your business for success in the competitive world of logistics and supply chain management.
Understanding System Directed Putaway

Definition and key components
System-driven putaway is a strategic approach to warehouse storage that uses data, technology, and predefined rules to determine the optimal location for each item.
Unlike traditional methods relying on human decision-making or simplistic zone-based storage, system-driven putaway considers multiple factors to maximize efficiency.
Key components of a system-driven putaway process include:
- Warehouse Management System (WMS): The central nervous system that collects and analyzes data, making storage decisions based on predefined rules.
- Item profiling: Detailed information about each SKU, including dimensions, weight, handling requirements, and demand patterns.
- Location profiling: This involves identifying the characteristics of each storage location, such as size, accessibility, and proximity to picking areas.
- Business rules engine: A set of configurable rules that determine storage locations based on various factors.
- Real-time inventory tracking: Accurate, up-to-date information on stock levels and available storage locations.
Benefits of implementing a system-driven approach
- Optimized space utilization: By considering item dimensions and storage location characteristics, system-driven putaway maximizes the use of available space.
- Improved picking efficiency: Strategic placement of items reduces travel time and streamlines the picking process.
- Reduced labor costs: With items stored optimally, less time and effort are required for both putaway and picking operations.
- Enhanced inventory accuracy: Systematic storage reduces errors and makes it easier to locate items.
- Increased throughput: Efficient storage and retrieval processes allow faster order fulfillment and higher warehouse throughput.
- Adaptability to changing conditions: System-driven putaway can quickly adapt to changes in inventory levels, seasonal fluctuations, or shifts in order patterns.
- Data-driven decision-making: The wealth of data generated by this approach provides valuable insights for continuous improvement.
- Improved worker satisfaction: System-driven putaway can make warehouse jobs less physically demanding and more satisfying by reducing unnecessary movement and making items easier to find.
By leveraging these components and reaping these benefits, warehouses can transform their operations from reactive to proactive, setting the stage for significant improvements in efficiency and cost-effectiveness.
In the next section, we’ll explore specific strategies for effective putaway and demonstrate how this system-driven approach can be applied to various types of inventory and picking methods.
Strategies for Effective Putaway

A system-driven putaway process can be tailored to various types of inventory and picking methods. Here are some key strategies for different scenarios:
Storing bulk items picked with forklifts
- Group similar items: Store bulk items typically picked together near reduce forklift travel time.
- Consider weight and stability: Place heavier items on lower levels for safety and ease of access.
- Optimize for FIFO: Arrange storage to facilitate first-in-first-out inventory management.
- Allow for easy access: Ensure adequate aisle width for forklift maneuverability.
Organizing bulk items picked as eaches
- Zone-based storage: Create dedicated areas for items frequently picked together, reducing travel time for pickers using carts or pallet jacks.
- Velocity-based slotting: Place fast-moving items in easily accessible locations, potentially closer to packing areas.
- Ergonomic considerations: Store heavier items at waist level to reduce picker strain.
- Implement batch picking: Organize storage to support efficient batch-picking routes.
Grouping conveyable cases for pick-to-belt or pick-to-pallet
- Proximity to conveyors: Store these items close to conveyor belts to minimize travel distance.
- Size and weight optimization: Arrange items so that larger, heavier cases don’t impede the flow of smaller ones.
- Frequency-based placement: Position high-turnover items for quick and easy access to the conveyor system.
- Consider order patterns: Group items often ordered together to streamline the picking process.
Arranging unit picks based on replenishment locations
- Vertical integration: Align unit pick locations with their respective bulk storage areas to simplify replenishment.
- Demand-based positioning: Place high-demand items in prime picking locations, considering both frequency and quantity of picks.
- Size-based organization: Group similarly sized items to maximize space utilization in pick areas.
- Replenishment route optimization: Arrange storage to create efficient replenishment paths, reducing restocking time.
By implementing these strategies, warehouses can significantly improve their putaway and picking processes. The key is to use the system to analyze data on item characteristics, order patterns, and operational workflows to determine the most efficient storage locations.
This approach optimizes the initial putaway process and sets the foundation for more efficient picking, replenishment, and warehouse operations.
The next section will explore how these strategies directly impact pick path optimization and operational efficiency.
Impact on Pick Path Optimization

A system-driven putaway process profoundly impacts pick path optimization, which is crucial for warehouse efficiency. Here’s how it affects key areas:
Reducing travel time and distance
- Clustered storage: By storing frequently picked items together, the system reduces the distance pickers need to travel between picks.
- Strategic item placement: High-velocity items are placed in easily accessible locations, minimizing travel time for the most common picks.
- Multi-zone picking: The system can support efficient multi-zone picking strategies, allowing pickers to work in designated areas and reducing congestion.
- Batch and wave picking optimization: Putaway strategies support more efficient batch and wave picking, allowing for optimized pick routes that cover multiple orders simultaneously.
- Vertical optimization: Proper placement of items across different shelf levels reduces the time spent moving between heights.
Improving order fulfillment speed
- Reduced search time: With items logically placed, pickers spend less time searching for products, speeding up the picking process.
- Improved accuracy: Logical placement reduces picking errors, minimizing time-consuming correction processes.
- Faster replenishment: When unit pick areas are aligned with bulk storage, replenishment becomes quicker and more efficient, reducing stock-outs and pick delays.
- Support for technology integration: Optimized storage layouts work seamlessly with pick-to-light, voice picking, or RF scanning technologies, further speeding up the picking process.
- Balanced workload: The system helps balance the workload across different picking zones or teams by strategically distributing high-demand items.
- Simplified consolidation: When items for the same orders are stored in proximity, it reduces the time and complexity of order consolidation.
The impact of these optimizations can be substantial:
- Studies have shown that optimized pick paths can reduce travel time by up to 50%.
- With proper slotting and putaway strategies, order fulfillment speed can increase by 20-30%.
- Picking accuracy can improve by up to 99.9%, dramatically reducing the time and cost associated with errors.
These improvements increase productivity and enhance customer satisfaction through faster, more accurate order fulfillment. Moreover, optimized pick paths reduce worker fatigue, potentially improving job satisfaction and reducing turnover.
In the next section, we’ll explore how these efficiencies translate directly into cost savings, demonstrating the tangible financial benefits of implementing a system-driven putaway process.
Cost Reduction Through Efficient Storage

Implementing a system-driven putaway process reduces costs across various aspects of warehouse operations. Here’s a breakdown of the key areas where you can expect to see savings:
Labor cost savings
- Reduced picking time: With optimized storage locations, pickers spend less time traveling and searching for items, increasing productivity and reducing labor hours.
- Efficient replenishment: Aligned storage areas for bulk and unit picks streamline the replenishment process, reducing the time and labor required.
- Decreased training time: Logical storage systems are easier for new employees to learn, reducing training costs and time to proficiency.
- Lower error rates: Improved accuracy in picking reduces the labor costs associated with correcting mistakes and processing returns.
- Overtime reduction: Increased efficiency often leads to less need for overtime during peak periods.
Equipment utilization improvements
- Optimized forklift usage: Strategic placement of bulk items reduces travel time, increasing productivity and potentially reducing the number of forklifts needed.
- Extended equipment lifespan: Less travel time means less wear and tear on equipment, potentially extending its useful life and reducing replacement costs.
- Reduced maintenance costs: With equipment being used more efficiently, maintenance needs and associated costs may decrease.
- Better utilization of automated systems: If your warehouse uses automated storage and retrieval systems, optimized putaway ensures these expensive systems are used to their full potential.
Space optimization benefits
- Increased storage density: By considering item dimensions and storage location characteristics, system-driven putaway can increase the amount of inventory stored in the same space.
- Reduced need for expansion: Better space utilization may delay or eliminate the need for costly warehouse expansions.
- Improved inventory turnover: Proper storage strategies can lead to better inventory management, reducing carrying costs.
- Flexible space utilization: The system can adapt to changing inventory needs, using available space better during seasonal fluctuations.
- Reduced aisle space: Optimized storage may allow for narrower aisles in some areas, increasing overall storage capacity.
The financial impact of these improvements can be substantial:
- Labor costs often account for 50-70% of warehouse operating expenses. Even a 10-20% reduction in labor needs can result in significant savings.
- Improved space utilization can increase storage capacity by 10-30% without physical expansion.
- Reductions in error rates can save 1-3% of a company’s annual revenue that would otherwise be lost to picking mistakes.
By implementing a system-driven putaway process, warehouses can achieve these cost reductions while improving operational efficiency and customer satisfaction. This creates a powerful competitive advantage in the fast-paced world of logistics and supply chain management.
The next section will explore the practical aspects of implementing a system-driven putaway process, including key considerations and potential challenges.
Implementing a System-Driven Putaway Process

While the benefits of a system-driven putaway process are clear, implementation requires careful planning and execution. Here’s a guide to help you navigate this process:
Key considerations
- Current state assessment: Evaluate your existing warehouse layout, processes, and pain points.
- Goal setting: Define clear, measurable objectives for the new system (e.g., reducing pick times by 25%, increasing storage capacity by 15%).
- Technology infrastructure: Assess your current warehouse management system (WMS) and determine if upgrades are needed.
- Data quality: Ensure you have accurate data on inventory, SKU characteristics, and historical order patterns.
- Change management: Plan for staff training and address potential resistance to new processes.
- Phased approach: Consider implementing the new system in stages to minimize disruption.
Potential challenges and solutions
- Integration with existing systems solution: Work closely with IT teams and vendors to ensure smooth integration. Consider middleware solutions if necessary.
- Initial productivity dip during transition solution: Plan for a temporary increase in labor during the transition period. Implement the change during a slower season if possible.
- Resistance from staff Solution: Involve key team members in the planning process. Communicate benefits clearly and provide comprehensive training.
- Dealing with exceptions and non-standard items: Develop clear protocols for handling exceptions. Ensure the system is flexible enough to accommodate special cases.
- Maintaining system accuracy over time: Implement regular audits and continuous improvement processes. Use cycle counting to maintain inventory accuracy.
Technology and software requirements
- Robust Warehouse Management System (WMS): This is the cornerstone of a system-driven putaway process. Ensure your WMS can handle complex putaway rules and integrate with other systems.
- Real-time location system (RTLS): Consider implementing RTLS for more accurate tracking of inventory and equipment.
- Mobile devices: Equip staff with mobile scanners or tablets to interact with the WMS in real-time.
- Data analytics tools: These will help you analyze performance and identify areas for ongoing improvement.
- Automated materials handling equipment: While not strictly necessary, automated storage and retrieval systems (AS/RS) or automated guided vehicles (AGVs) can further enhance the efficiency of your system-driven putaway process.
- Slotting optimization software: This can help you continually refine your storage strategies based on changing demand patterns.
Implementing a system-driven putaway process is a significant undertaking, but with proper planning and execution, it can transform your warehouse operations.
The key is to approach the implementation as a continuous improvement process, regularly reviewing and refining your strategies based on data and feedback.
Case Study: Success in Action

To illustrate the real-world impact of implementing a system-driven putaway process, let’s examine the case of MegaStore Distributors, a mid-sized e-commerce fulfillment center.
Company background and initial challenges
MegaStore Distributors operates a 200,000-square-foot warehouse, handling approximately 20,000 SKUs and processing an average of 5,000 orders per day. Before implementing a system-driven putaway process, they faced several challenges:
- High labor costs due to inefficient picking routes
- Frequent stockouts of popular items
- Difficulty in managing seasonal inventory fluctuations
- Rising error rates, especially during peak periods
- Increasing customer complaints about slow order fulfillment
Implementation of system-driven putaway
MegaStore decided to overhaul its warehouse operations with a system-driven putaway process. Their implementation strategy included:
- Upgrading their WMS to support advanced putaway rules and real-time inventory tracking
- Conducting a thorough analysis of their SKU characteristics and order patterns
- Redesigning their warehouse layout to support more efficient storage and picking
- Implementing a zone-based picking system supported by the new putaway process
- Training staff on the new system and processes
- Phasing in the new system over three months to minimize disruption
Key features of their new putaway system included
- Storing fast-moving items in easily accessible locations near packing areas
- Grouping frequently co-ordered items together
- Aligning bulk storage areas with their corresponding unit pick locations
- Implementing a dynamic slotting system that adjusts to seasonal demand changes
Results and ROI
After six months of operating with the new system-driven putaway process, MegaStore Distributors saw significant improvements:
- Labor efficiency:
- Picking productivity increased by 30%
- Labor costs reduced by 22%
- Space utilization:
- Storage capacity increased by 15% without physical expansion
- Seasonal inventory fluctuations managed without additional offsite storage
- Accuracy and customer satisfaction:
- Order accuracy improved from 97% to 99.5%
- Customer complaints regarding delayed orders decreased by 60%
- Inventory management:
- Stockouts of high-demand items reduced by 70%
- Inventory turns increased by 25%
- Overall efficiency:
- Order fulfillment time reduced by 40%
- Able to handle 30% more daily orders with existing staff
Financial impact
- The project cost $500,000 to implement, including software upgrades and consulting fees
- Annual savings in labor and operational costs: $1.2 million
- ROI achieved in less than 6 months
MegaStore Distributors’ success demonstrates the transformative potential of a well-implemented system-driven putaway process. By strategically reorganizing their warehouse and leveraging data to optimize storage and picking, they significantly improved efficiency, reduced costs, and enhanced customer satisfaction.
This case study underscores the tangible benefits of a system-driven warehouse management approach, providing a compelling argument for other companies considering similar implementations.
Best Practices and Tips

To maximize the benefits of a system-driven putaway process and ensure its long-term success, consider the following best practices and tips:
Continuous improvement strategies
- Regular data analysis:
- Continuously analyze your inventory and order data to identify trends and opportunities for optimization.
- Use key performance indicators (KPIs) such as pick rates, travel time, and order accuracy to measure improvements.
- Periodic re-slotting:
- Conduct regular re-slotting exercises to account for changes in demand patterns or product mix.
- Consider using slotting optimization software to automate this process.
- Feedback loops:
- Establish a system for warehouse staff to provide feedback on the putaway and picking processes.
- Regularly review and act on this feedback to refine your strategies.
- Stay updated on technology:
- Keep abreast of new technologies in warehouse management and consider how they might enhance your system.
- Regularly evaluate your WMS and consider upgrades when beneficial.
- Seasonal adjustments:
- Develop strategies for adjusting your putaway rules to accommodate seasonal fluctuations in demand.
Staff training and adaptation
- Comprehensive initial training:
- Provide thorough training on the new system and processes before implementation.
- Include both theoretical knowledge and hands-on practice.
- Ongoing education:
- Offer regular refresher courses and training on system updates.
- Cross-train employees on different aspects of the warehouse operation to increase flexibility.
- Clear communication:
- Ensure all staff understand the reasons behind the system-driven approach and its benefits.
- Regularly communicate performance improvements to maintain motivation.
- Empowerment:
- Encourage staff to suggest improvements based on their day-to-day experiences.
- Recognize and reward valuable contributions to the system’s efficiency.
- Change management:
- Anticipate and address resistance to change through open communication and involvement.
- Identify and support “champions” who can help drive adoption among their peers.
Additional Tips
- Start small: If you’re new to system-driven putaway, consider starting with a pilot program in one area of your warehouse before full implementation.
- Leverage vendor expertise: Work closely with your WMS vendor or consider hiring consultants with expertise in warehouse optimization.
- Plan for exceptions: While your system should handle most situations automatically, have clear procedures in place for dealing with exceptions.
- Maintain data integrity: Implement rigorous processes for maintaining accurate inventory data, as this is crucial for the system’s effectiveness.
- Balance efficiency with ergonomics: While optimizing for efficiency, don’t forget to consider the physical demands on your staff. Ensure frequently picked items are stored at comfortable heights.
- Future-proof your system: When implementing your system, consider potential future needs such as expansion or the addition of new product lines.
- Integrate with other systems: Ensure your putaway system integrates smoothly with other warehouse systems such as receiving, shipping, and returns processing.
By following these best practices and tips, you can ensure that your system-driven putaway process continues to deliver value over time, adapting to changing needs and consistently driving efficiency in your warehouse operations.

Conclusion
In today’s fast-paced, competitive business environment, warehouse efficiency is no longer a luxury—it’s a necessity. A system-driven putaway process is a powerful tool for achieving this efficiency, offering a strategic approach to one of the most fundamental aspects of warehouse operations: where and how items are stored.
Throughout this blog, we’ve explored how this approach can dramatically improve various aspects of warehouse management:
- Optimizing space utilization
- Reducing labor costs
- Improving pick path efficiency
- Enhancing inventory accuracy
- Boosting overall operational productivity
The MegaStore Distributors case study vividly illustrates this approach’s transformative potential, demonstrating substantial improvements in efficiency, cost reduction, and customer satisfaction.
However, implementing a system-driven putaway process is not a one-time event but an ongoing optimization journey. It requires a commitment to continuous improvement, leveraging data analytics, and fostering a culture of adaptability among your workforce.
As we look to the future, the importance of efficient warehouse operations will only grow. E-commerce continues to expand, customer expectations for rapid fulfillment are rising, and competition in the logistics sector is intensifying.
In this context, a system-driven putaway process isn’t just an operational improvement—it’s a strategic advantage that can position your business for long-term success.
Call to Action

The benefits of a system-driven putaway process are clear, but the journey begins with a single step. Here’s what you can do to start optimizing your warehouse operations:
- Assess your current operations: Critically examine your existing putaway and picking processes, identifying pain points and inefficiencies.
- Set clear goals: Define your goal with a system-driven approach. Is it labor cost reduction, improved order accuracy, faster fulfillment times, or all of the above?
- Evaluate your technology: Does your current WMS support advanced putaway rules? If not, research potential upgrades or new systems.
- Engage your team: Discuss the potential changes with your warehouse staff. Their insights can be invaluable in planning and implementation.
- Consider expert help: If the task seems daunting, don’t hesitate to seek assistance from consultants or vendors specializing in warehouse optimization.
- Start planning: Plan a roadmap for implementing a system-driven putaway process in your warehouse.
Remember, the path to warehouse efficiency is a journey, not a destination. By taking these first steps towards a system-driven putaway process, you’re setting your organization on a course for continuous improvement and competitive advantage.
Don’t let inefficiencies in your warehouse hold your business back. Start your journey towards optimized operations today, and position your company for success in the dynamic world of modern logistics.
Related
Discover more from Warehouse Whisper
Subscribe to get the latest posts sent to your email.
One Comment